Unlocking Efficiency: The Strategic Value of Total Productive Maintenance (TPM)
In today’s competitive industrial landscape, organizations must relentlessly pursue operational efficiency to stay ahead. One of the most impactful methodologies to support this objective is Total Productive Maintenance (TPM). Grounded in the philosophy of proactive and preventive maintenance, TPM is designed to maximize equipment effectiveness and foster a culture of continuous improvement. As Mark Twain once said: "Continuous improvement is better than delayed perfection."
What Is Total Productive Maintenance (TPM)?
TPM is a holistic approach to equipment maintenance that aims to achieve perfect production: zero unplanned downtime, zero defects, and zero accidents. Unlike traditional maintenance strategies that rely solely on dedicated maintenance staff, TPM involves everyone in the organization—from operators to senior management—in maintaining and improving equipment.
Developed in Japan in the 1970s and later adopted worldwide, TPM is built around eight foundational pillars:
1. Autonomous Maintenance
2. Planned Maintenance
3. Focused Improvement
4. Quality Maintenance
5. Early Equipment Management
6. Training and Education
7. Safety, Health, and Environment
8. TPM in Administration
Together, these pillars create a structured framework for sustainable performance enhancement across the entire operation.
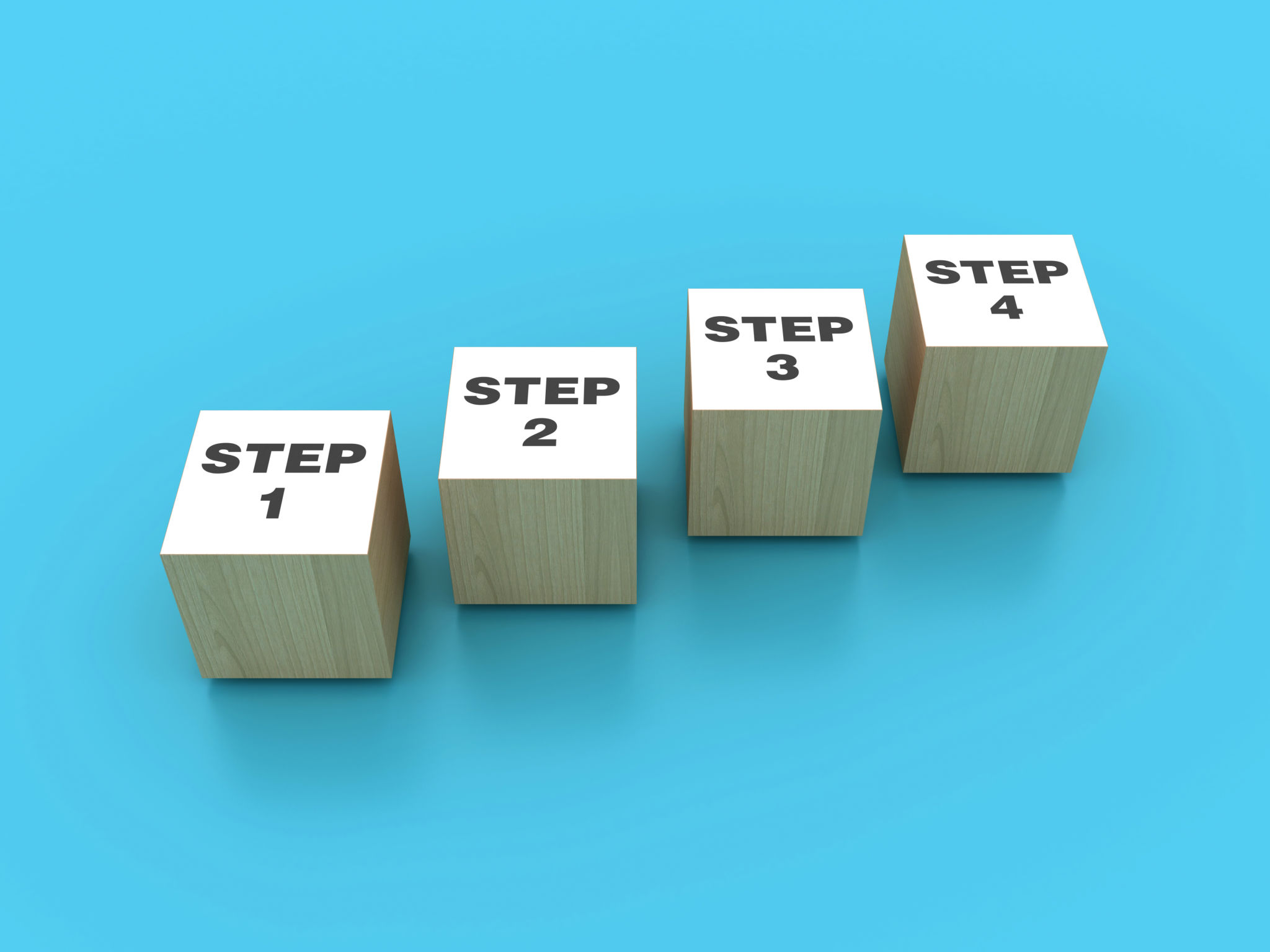
Implementing TPM: A Step-by-Step Approach
Implementing TPM is a multi-phase journey that requires cultural transformation, cross-functional collaboration, and consistent management support. Key implementation strategies include:
1. Top-Down Commitment
Leadership must champion the initiative and allocate the necessary resources. TPM is not a one-off project; it is a long-term commitment to operational excellence.
2. Initial Equipment Assessment
Organizations must first identify existing inefficiencies and failure modes. This includes evaluating unplanned downtime, frequent repairs, and quality issues.
3. Operator Involvement and Training
Operators are trained to perform basic maintenance tasks such as cleaning, lubricating, and inspecting their equipment. This promotes ownership and enables maintenance teams to focus on more complex issues.
4. Developing Maintenance Schedules
Planned and predictive maintenance routines are established based on equipment condition and usage. The goal is to address issues before they escalate.
5. Continuous Improvement Teams
Cross-functional teams are created to address recurring problems using root cause analysis and problem-solving techniques like 5 Whys and Fishbone Diagrams.
6. Performance Monitoring
Overall Equipment Effectiveness (OEE) becomes the primary KPI, measuring performance, availability, and quality.
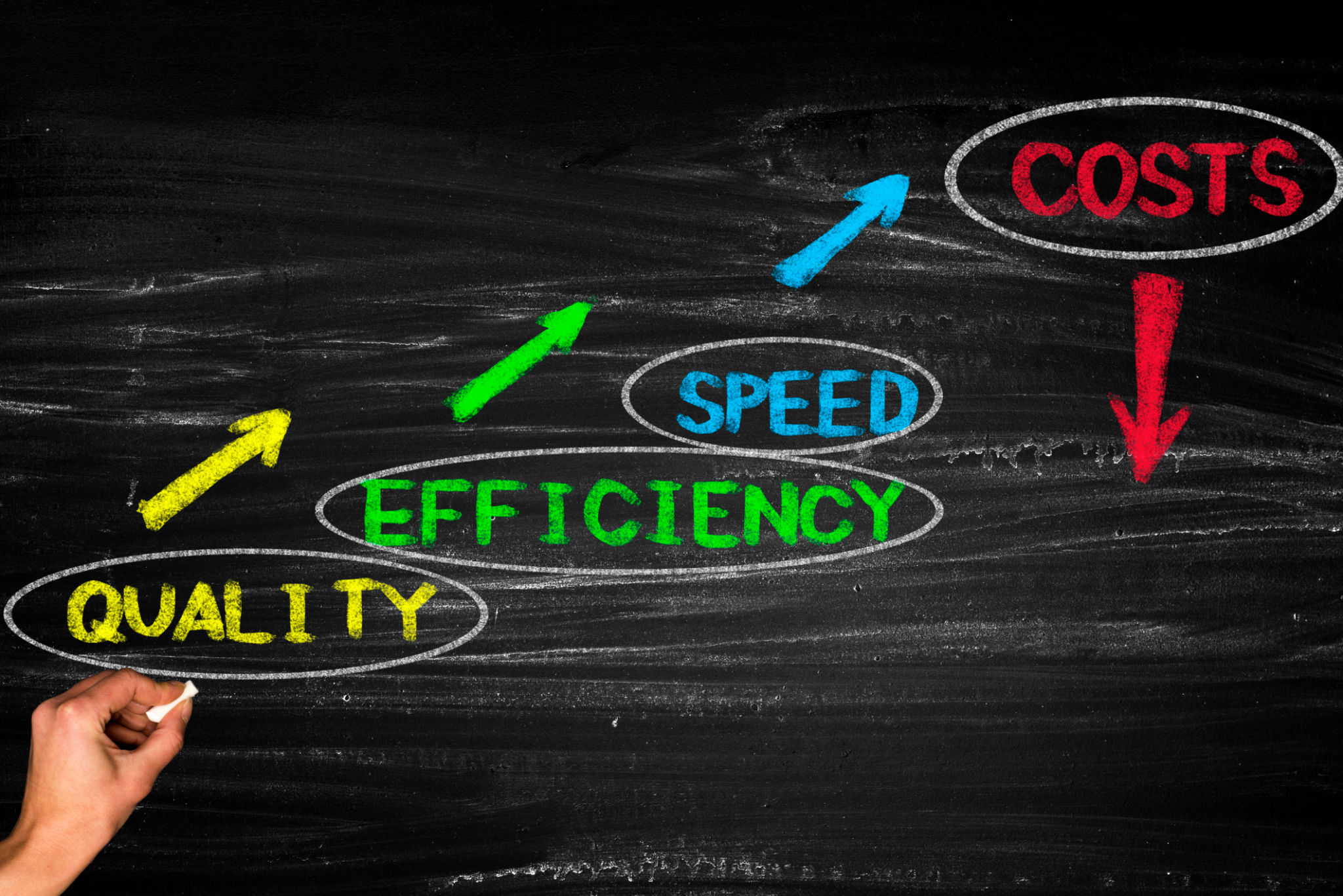
The Impact of TPM on Overall Equipment Effectiveness
TPM has a direct and measurable impact on Overall Equipment Effectiveness (OEE), the gold standard for asset performance. According to the Lean Enterprise Institute (2017), companies implementing TPM see an average 25% increase in OEE.
Improvements include:
o Higher Availability: Equipment is operational when needed, with fewer breakdowns.
o Better Performance: Machines operate at optimal speed without slowdowns.
o Improved Quality: Fewer defects and rework increase first-pass yield.
These gains translate into:
o Lower maintenance costs
o Increased production capacity
o Extended asset lifespan
o Improved safety records
Supporting this, McKinsey & Company (2020) reported that advanced maintenance strategies like TPM can reduce maintenance costs by 20-30% and increase asset utilization by 10-15%.
Common Challenges and How to Overcome Them
Implementing TPM is not without its problems. Resistance to change, lack of training, and insufficient leadership support are common barriers. These can be addressed by:
o Effective Change Management: Communicate the why behind TPM and celebrate early wins.
o Tailored Training Programs: Upskill staff at all levels to build competence and confidence.
o KPI Transparency: Use dashboards to track progress and demonstrate ROI.
There will be bumps in the road as things won’t go as planned, things will change too slowly, or there will be unforeseen obstacles that will require addressing. The key is to keep focus on the goal, work the process, and be transparent.
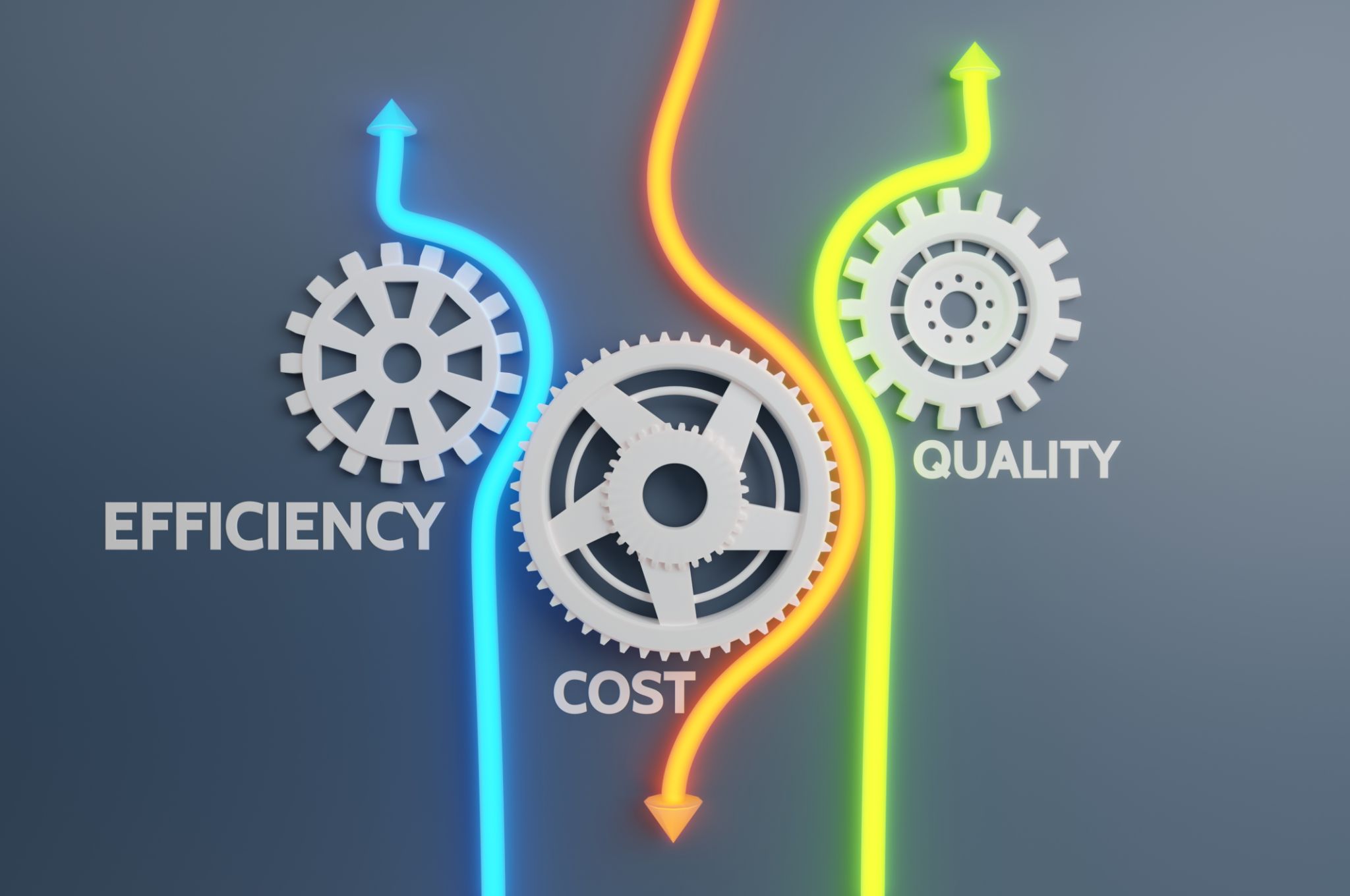
Call to Action:
Total Productive Maintenance is more than a maintenance program—it's a culture shift that unlocks peak efficiency. At RPC Maint, we can help you in designing and implementing TPM frameworks tailored to your unique operational goals.
Let us help you turn equipment reliability into a competitive advantage. Partner with RPC Maint and start your TPM journey today.
#TPM #ProductiveMaintenance #EquipmentEffectiveness