Transforming Maintenance Management for Operational Excellence
Implementing effective maintenance management is not just a technical upgrade: it is a strategic shift that drives measurable business outcomes. This case study presents a real-world example of how a mid-sized manufacturing company overcame critical operational challenges through a tailored maintenance management solution. As Albert Schweitzer once said, "Success is not the key to happiness. Happiness is the key to success."
The Challenge: Inefficiency, Downtime, and Rising Costs
A regional manufacturer of industrial components, faced mounting maintenance issues that were impacting productivity, safety, and profitability. Key challenges included:
1. Unscheduled Downtime: Equipment failures were causing frequent production stoppages.
2. Reactive Maintenance Culture: Over 75% of maintenance activity was reactive, leading to inefficiencies and elevated repair costs.
3. Lack of Visibility: No centralized data system for tracking maintenance history, asset performance, or technician utilization.
4. Compliance Gaps: Safety and regulatory compliance were at risk due to inconsistent documentation and missed inspections.
These issues contributed to lost revenue, decreased asset reliability, and poor workforce morale. The leadership team recognized that a systemic transformation was required to address the root causes.

The Solution: A Strategic Maintenance Management Overhaul
A comprehensive operational audit was conducted to assess current practices and identify opportunities for optimization. Based on this evaluation, the following strategic initiatives were implemented:
1. Deployment of a Computerized Maintenance Management System (CMMS)
A scalable CMMS was customized and deployed to centralize maintenance data and automate workflows. Features included:
o Digital work orders and maintenance schedules
o Asset tracking with performance logs
o Technician time and task management
o Automated compliance checklists
2. Shift to Preventive and Predictive Maintenance
Using a combination of FMECA, RCM, and in-house expertise, the maintenance focus was moved from reactive to proactive asset care. This included:
o Preventive maintenance routines based on manufacturer specs + experience
o Vibration, thermal, and oil sampling analyses for predictive insights
o Condition monitoring sensors for critical equipment integrated with the CMMS
3. Workforce Training and Communication Enhancement
Technical training was provided to all maintenance personnel on new processes, systems, and safety protocols. Communication protocols were also standardized:
o Shift handover checklists
o Daily planning meetings
o Root cause analysis (RCA) debriefs for failures
4. KPI Development and Performance Monitoring
Key performance indicators were introduced to measure maintenance effectiveness, including:
o Mean Time Between Failures (MTBF)
o Mean Time To Repair (MTTR)
o Schedule Compliance
o Maintenance Cost as a Percentage of Replacement Asset Value (RAV)
Weekly dashboard reviews enabled leadership to make data-driven decisions and hold teams accountable.
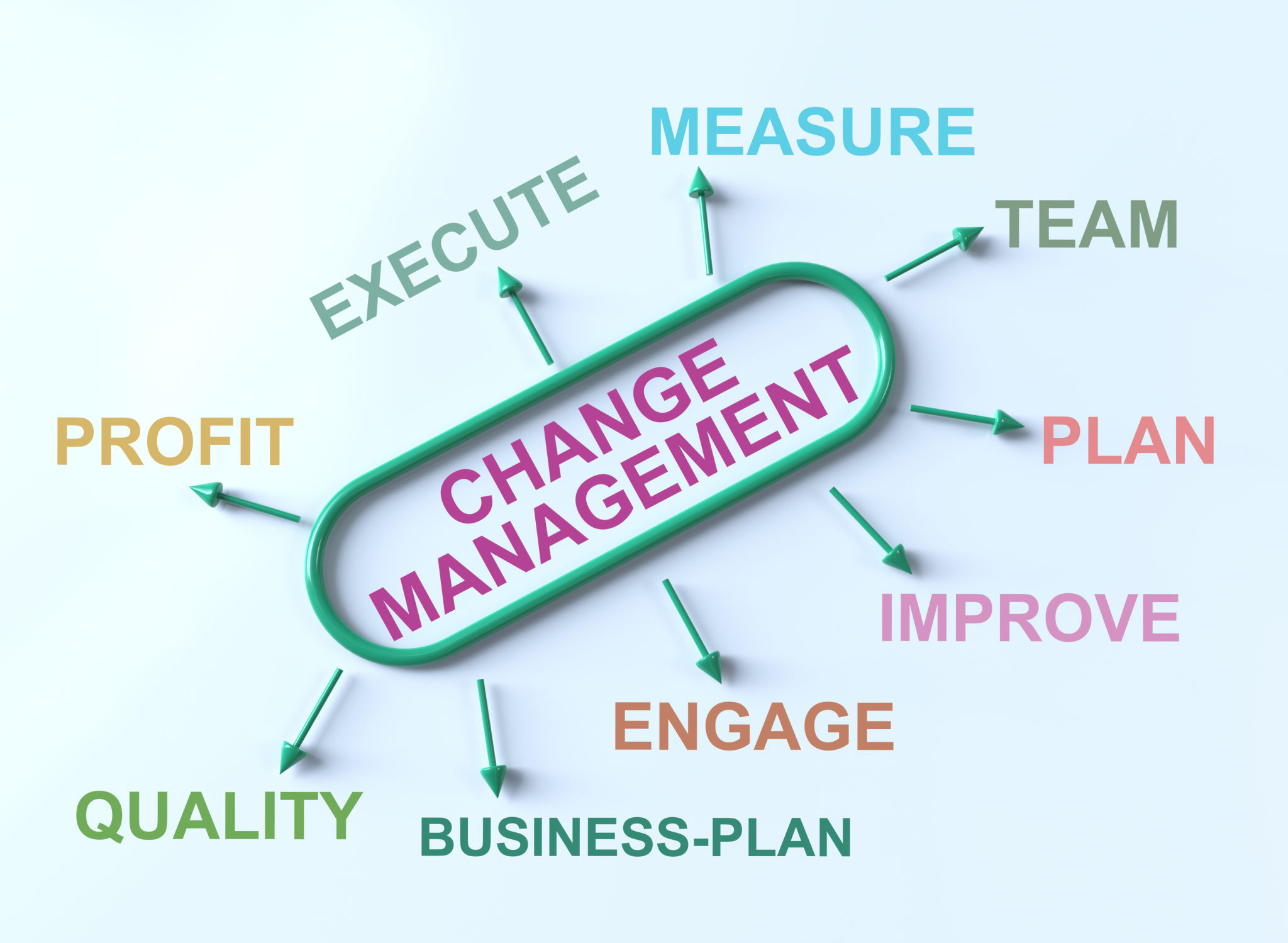
The Results: Increased Reliability, Reduced Costs, and Operational Visibility
Within 12 months of implementation, the client achieved significant performance improvements:
1. 30% Increase in Equipment Availability: Consistent with ARC Advisory Group (2018), the shift to proactive maintenance directly improved asset uptime.
2. 25% Reduction in Maintenance Costs: Fewer emergency repairs and optimized resource allocation led to cost savings.
3. 40% Reduction in Downtime: Planned maintenance and predictive interventions minimized disruption.
4. Improved Compliance: 100% audit readiness was achieved through digitized inspection records and automated reminders.
5. Boosted Workforce Engagement: Training and structured communication improved morale and reduced turnover.
Beyond the metrics, the client gained confidence in their operational resilience and future readiness. Maintenance was no longer a reactive cost center but a strategic enabler of business continuity.
Lessons Learned and Key Takeaways
This case study highlights several universal insights applicable across industries:
o Visibility Drives Accountability: What gets measured gets managed. Real-time data enables proactive decision-making.
o Training Empowers Technicians: Investment in workforce development pays dividends in quality, safety, and retention.
o Technology is an Enabler, Not a Silver Bullet: Systems must be integrated with strategy and culture to succeed.
o Maintenance is a Business Strategy: Reliable assets mean reliable output, which drives customer satisfaction and profitability.
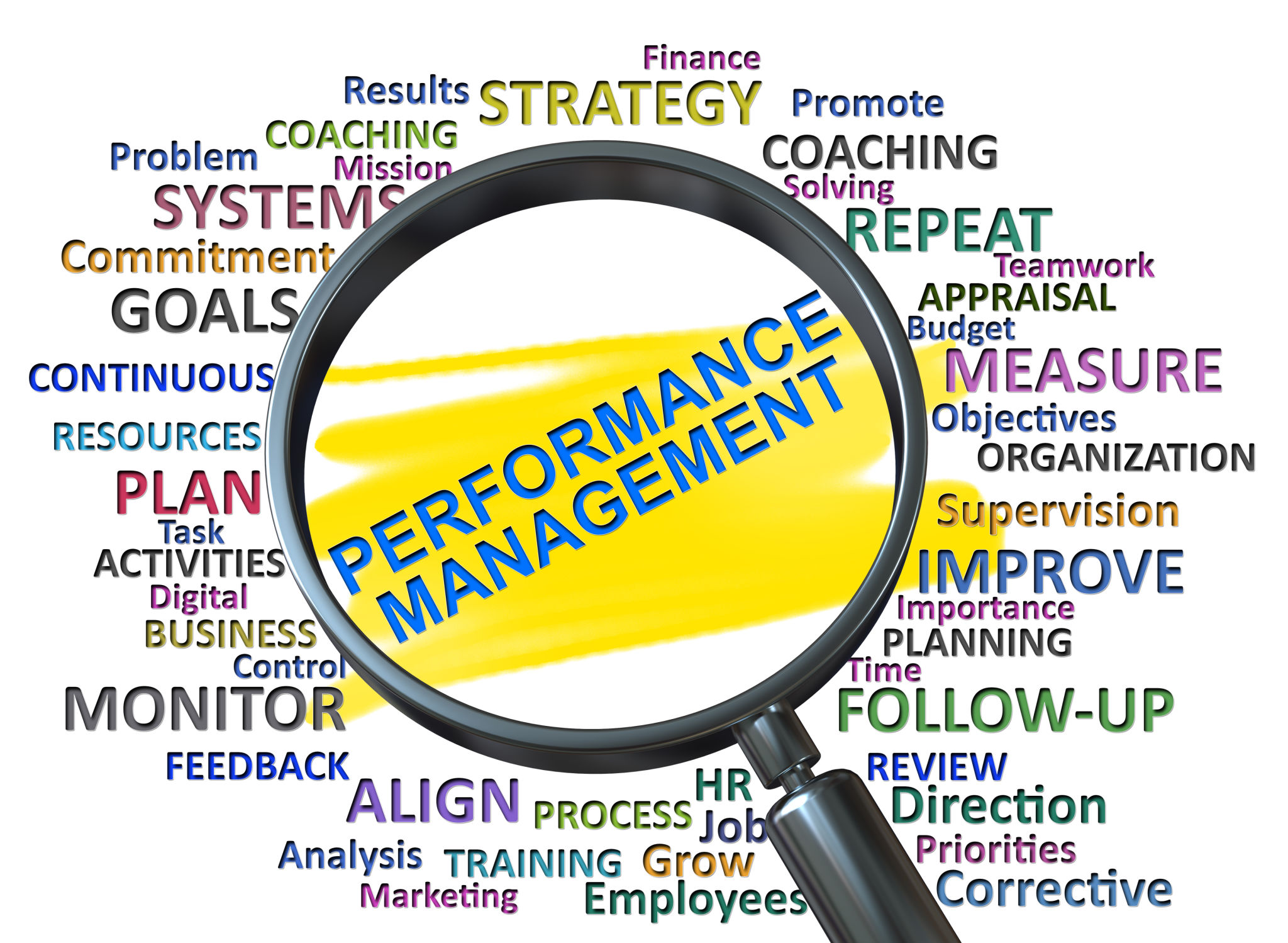
Call to Action:
Maintenance excellence doesn't happen by chance. It requires vision, expertise, and execution. RPC Maint specializes in designing and implementing strategic maintenance solutions tailored to your operational needs. From CMMS deployment and predictive analytics to training and KPI development, we deliver results that move the needle.
Let RPC Maint help you transform maintenance from a pain point into a performance driver. Contact us today to start your journey toward operational excellence.
#CaseStudy #MaintenanceSuccess #BestPractices