The Role of Effective Communication in Maintenance Teams
In maintenance management, effective communication is not just a soft skill—it is a mission-critical capability. Whether it involves coordinating shift handovers, detailing technical procedures, or ensuring safety protocols are understood, communication plays a fundamental role in operational reliability. As John Powell aptly noted, "Communication works for those who work at it."
Poor communication is a root cause of preventable maintenance errors, inefficiencies, and safety incidents. According to Harvard Business Review (2019), effective communication can reduce maintenance errors by 15%. This statistic underscores the tangible benefits of strengthening communication across maintenance operations.
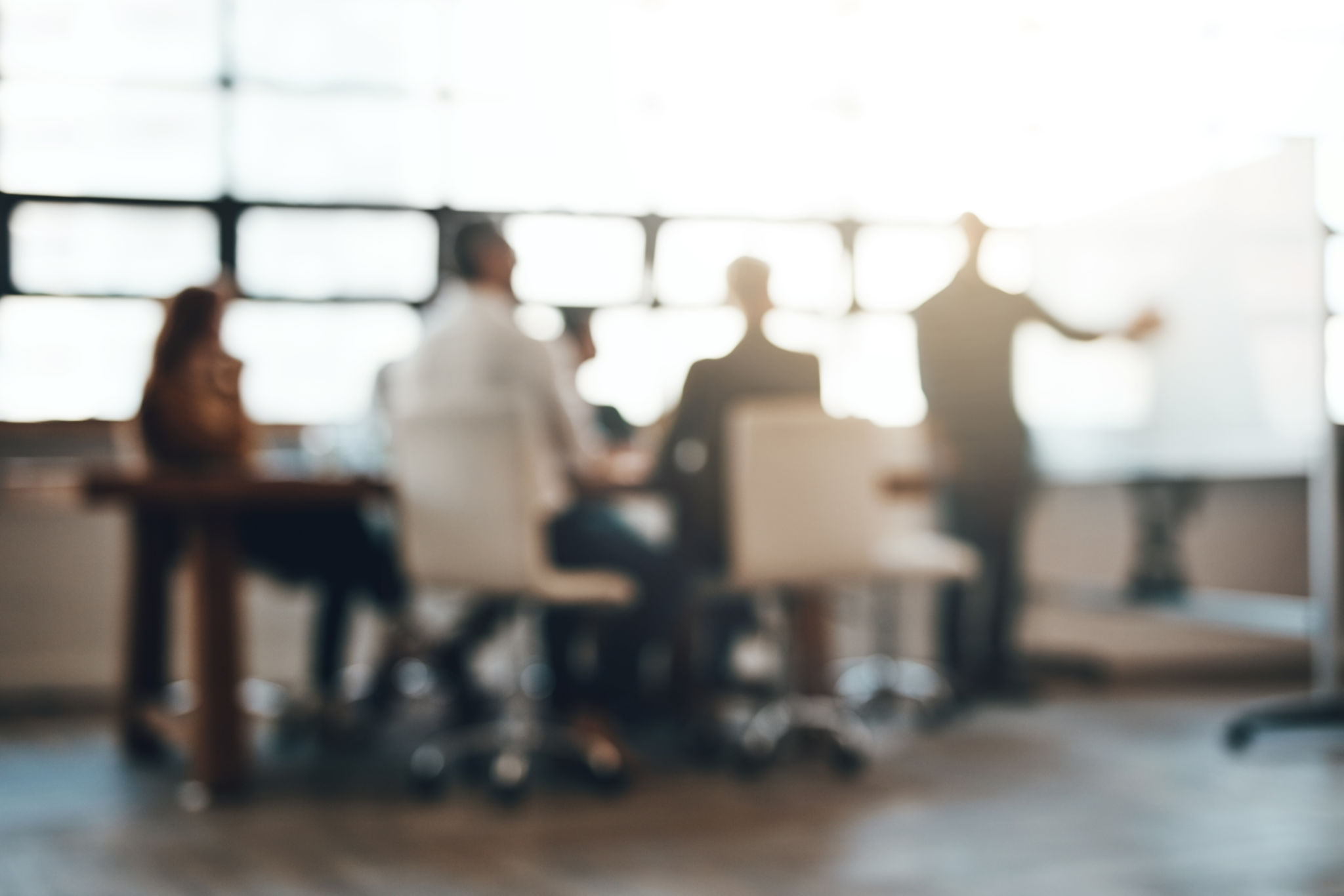
Why Communication Matters in Maintenance
Maintenance environments are inherently complex, involving multidisciplinary teams, rotating shifts, and time-sensitive decisions. Clear and consistent communication enables:
o Error Reduction: Misunderstandings in work orders or safety instructions can lead to costly or dangerous errors.
o Faster Response Times: Accurate information exchange accelerates issue resolution.
o Greater Accountability: Clear task delegation ensures that team members understand their responsibilities.
o Enhanced Safety: Precise communication of hazards, lockout-tagout (LOTO) procedures, and PPE requirements mitigates safety risks.
Techniques for Improving Communication in Maintenance Teams
1. Standardized Communication Protocols
Implementing structured methods for conveying information reduces ambiguity and promotes consistency. Examples include:
o Shift Handover Templates: Ensure seamless transitions by documenting key updates and pending tasks.
o Standard Operating Procedures (SOP): Provide step-by-step guides to minimize interpretation errors.
o Checklists: Facilitate task completion accuracy and consistency.
2. Digital Communication Tools
Modern technology streamlines communication across maintenance functions. Useful tools include:
o CMMS Platforms: Centralize work orders, maintenance logs, and status updates.
o Mobile Apps: Allow technicians to report issues, upload photos, and receive real-time feedback from remote teams.
o Digital Dashboards: Offer visibility into key performance metrics and asset conditions.
By digitizing communication, teams reduce dependency on verbal updates and handwritten logs, both of which are prone to errors and misinterpretation.
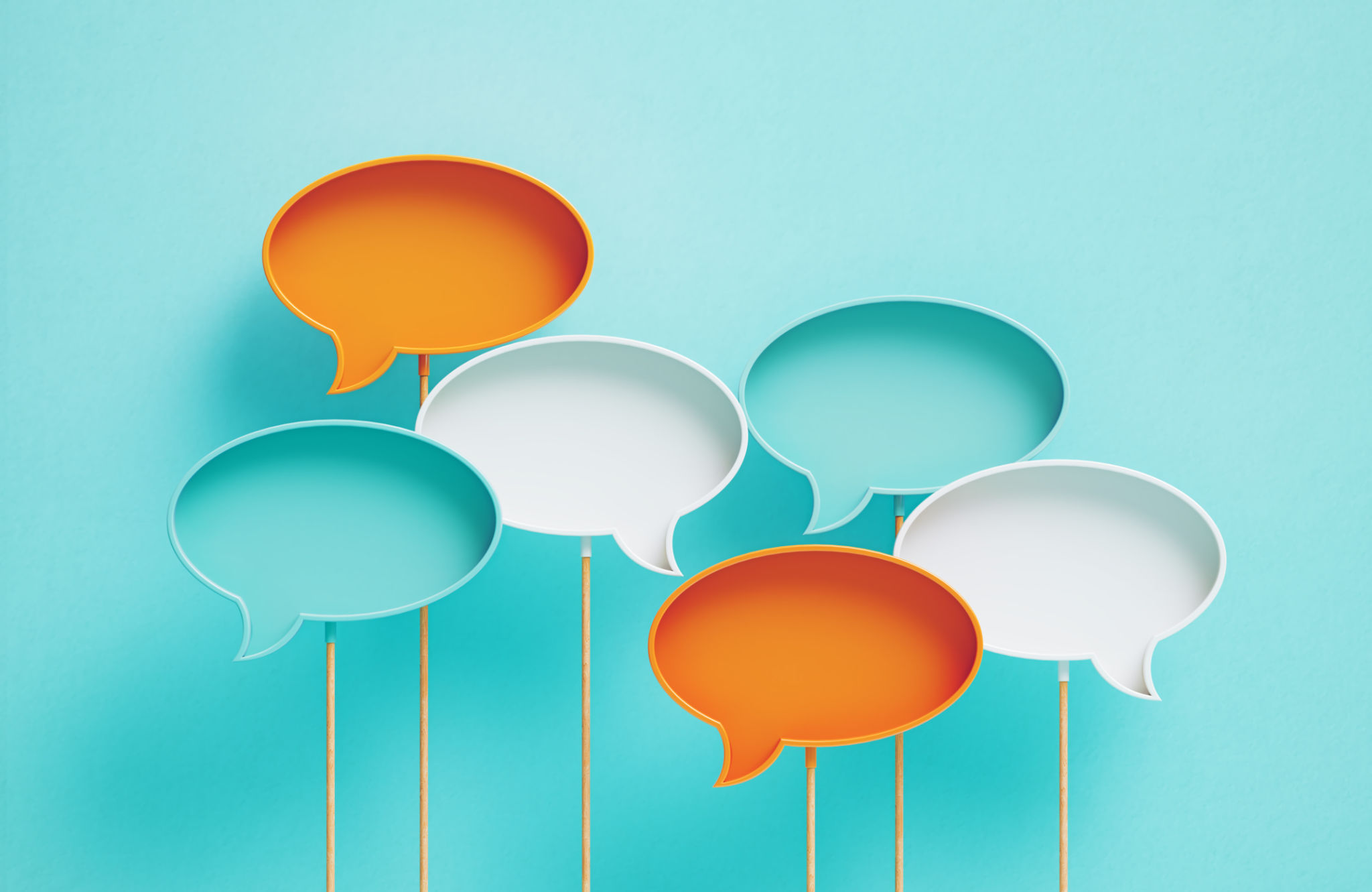
3. Regular Team Briefings and Debriefs
Scheduled briefings improve alignment and foster a culture of open dialogue. Effective practices include:
o Daily Kick-Off Meetings: Discuss shift goals, equipment statuses, and safety concerns.
o Post-Maintenance Reviews: Reflect on recent activities to identify successes and improvement areas.
o Toolbox Talks: Deliver short, focused safety or technical updates to reinforce learning.
4. Training in Communication Skills
Technical proficiency must be matched with interpersonal competence. Training modules in communication should include:
o Active Listening: Encourages mutual understanding.
o Clarity and Conciseness: Reduces misinterpretation of technical data.
o Feedback Mechanisms: Builds trust and continuous improvement.
Teams that communicate well are better prepared to handle the dynamic nature of maintenance work.
5. Visual Communication Aids
Visual tools support comprehension, especially in multilingual or high-noise environments:
o Color-Coded Tags and Labels: Clarify system status or hazards.
o Infographics and Flowcharts: Break down complex procedures.
o Digital Screens in Workshops: Broadcast safety alerts and real-time KPI.
These aids reduce cognitive load and provide immediate clarity in operational environments.
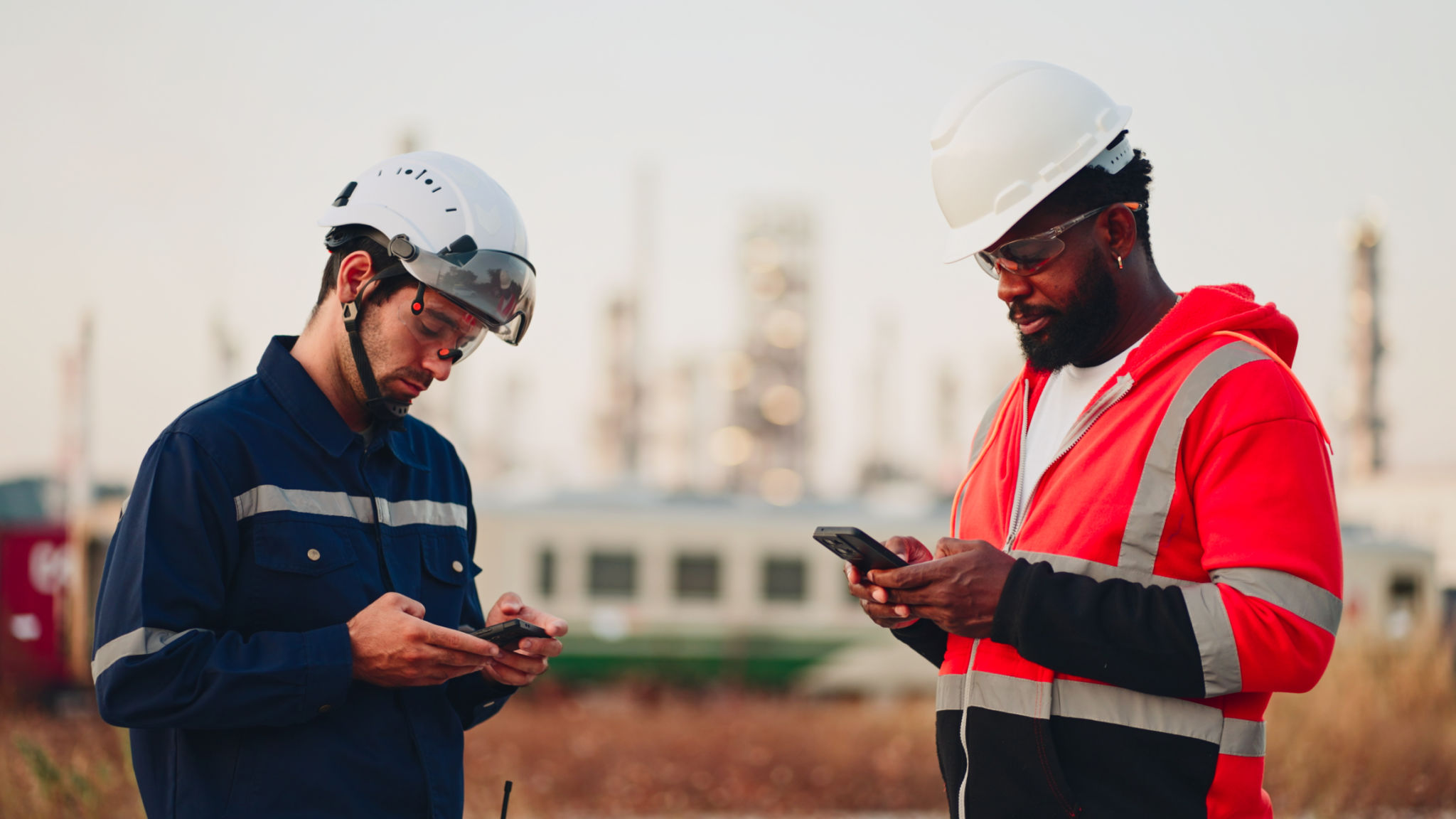
Benefits of Effective Communication
When communication is embedded as a core maintenance function, the benefits are substantial:
o Improved Equipment Reliability: Miscommunication-induced failures are significantly reduced.
o Stronger Safety Culture: Everyone is informed and vigilant.
o Higher Morale and Engagement: Technicians feel heard, respected, and aligned.
o Optimized Workflows: Better coordination leads to faster, error-free execution.
Ultimately, the ROI of strong communication is seen in reduced rework, fewer incidents, and more reliable operations.
Call to Action:
RPC Maint understands that world-class maintenance outcomes begin with world-class communication. Our consultants provide customized communication frameworks, training programs, and technology integration strategies that ensure your maintenance teams operate in lockstep.
Partner with RPC Maint to reduce errors, boost collaboration, and embed communication excellence into your maintenance culture. It’s time to talk the talk—and walk the walk. Contact us today.
#EffectiveCommunication #Teamwork #MaintenanceManagement