The Key Performance Indicators (KPI) for Maintenance Management: Measuring Success and Driving Improvement
Peter Drucker, one of the most influential management thinkers, once said, "What gets measured gets managed." This principle is particularly relevant in maintenance management, where well-defined Key Performance Indicators (KPI) can mean the difference between operational efficiency and costly downtime.
Research by IBM (2018) shows that companies utilizing KPI see a 20% improvement in their maintenance performance, highlighting the vital role of measurement in maintenance success.
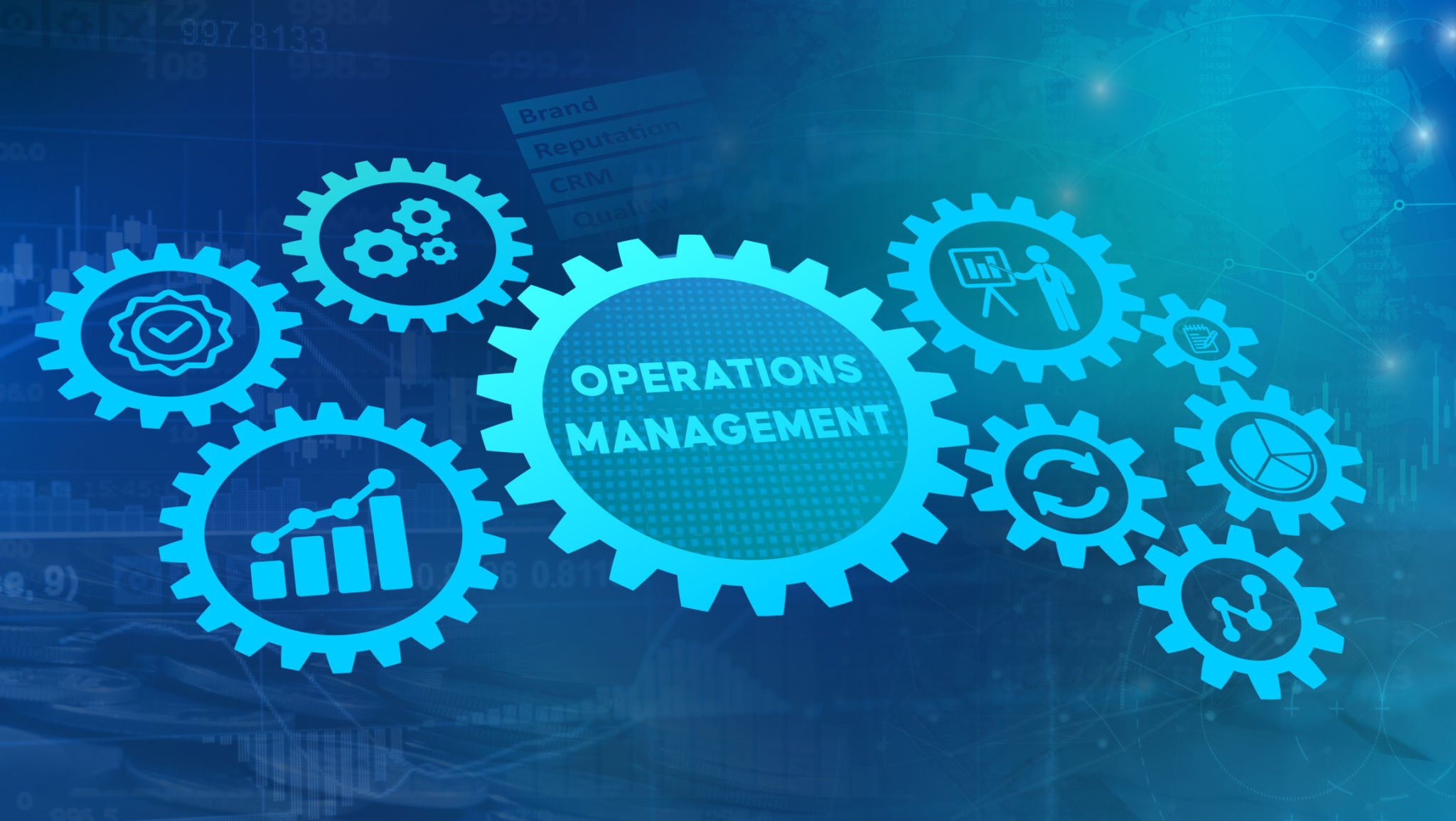
Why KPI Matter in Maintenance Management
KPI provide measurable benchmarks that enable organizations to track performance, optimize resource allocation, and ensure equipment reliability. By monitoring the right metrics, maintenance teams can:
- Identify inefficiencies and areas for improvement
- Reduce equipment failures and unplanned downtime
- Improve overall asset reliability and longevity
- Enhance cost control and budget management
- Ensure compliance with safety and regulatory standards
Essential KPI for Maintenance Management
There are numerous KPIs available to maintenance managers, covering various aspects of maintenance performance. While the number may vary depending on industry and business priorities, some of the most commonly tracked KPI include:
1. Reliability Metrics
o Mean Time Between Failures (MTBF)
o Mean Time to Repair (MTTR)
o Overall Equipment Effectiveness (OEE)
2. Work Management Metrics
o Planned Maintenance Percentage (PMP)
o Work Order Compliance (WOC)
o Schedule Compliance
3. Financial Metrics
o Maintenance Cost as a Percentage of Replacement Asset Value (RAV)
o Maintenance Budget Variance
o Cost per Work Order
4. Efficiency & Productivity Metrics
o Wrench Time (Productive Maintenance Time)
o Downtime as a Percentage of Operating Time
o Backlog of Work Orders
5. Safety & Compliance Metrics
o Number of Maintenance-Related Incidents
o Environmental Compliance Rate
Depending on the business goals and industry, maintenance managers may track anywhere from 10 to 50 KPI to ensure effective asset management and operational efficiency. However, the key is to identify and focus on the most relevant indicators that align with organizational objectives.
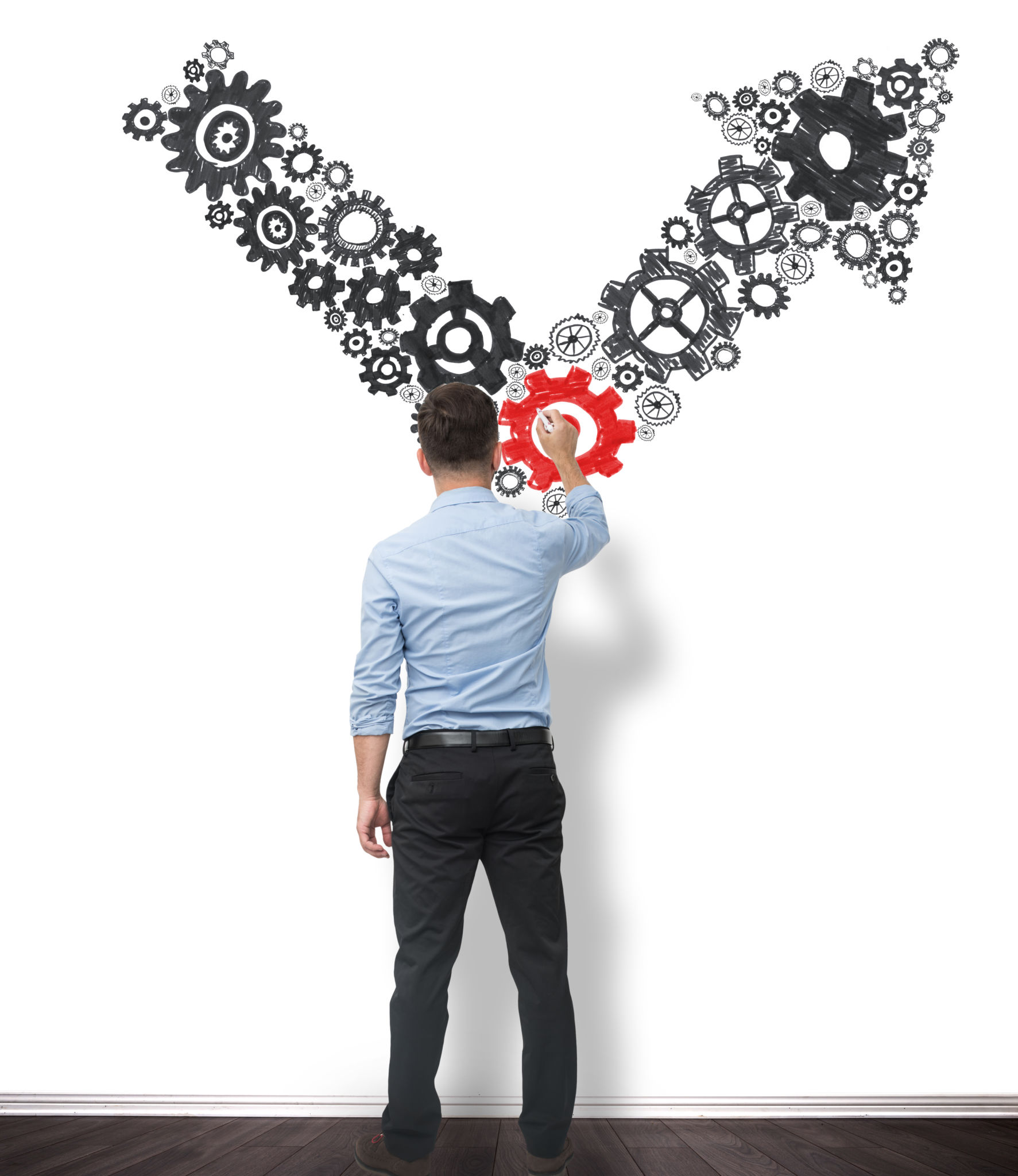
1. Mean Time Between Failures (MTBF)
Definition: MTBF measures the average time between equipment failures, indicating asset reliability.
How to Measure:
Importance: A higher MTBF suggests greater equipment reliability and fewer interruptions to production.
2. Mean Time to Repair (MTTR)
Definition: MTTR quantifies the average time taken to repair a failed asset and restore it to operational condition.
How to Measure:
Importance: Lower MTTR values indicate faster response times, minimizing production losses.
3. Planned Maintenance Percentage (PMP)
Definition: PMP calculates the proportion of maintenance work that is scheduled rather than reactive.
How to Measure:
Importance: A high PMP percentage ensures a proactive approach, reducing unexpected breakdowns and improving efficiency.
4. Overall Equipment Effectiveness (OEE)
Definition: OEE measures the overall performance of equipment by evaluating availability, performance, and quality.
How to Measure:
Importance: A high OEE score indicates that equipment is being utilized optimally with minimal waste and downtime.
5. Maintenance Cost as a Percentage of Replacement Asset Value (RAV)
Definition: This KPI assesses maintenance spending relative to the total value of assets.
How to Measure:
Importance: Keeping this percentage within industry benchmarks ensures maintenance spending is cost-effective without underfunding asset care.
6. Work Order Compliance (WOC)
Definition: WOC tracks the percentage of scheduled maintenance tasks completed on time.
How to Measure:
Importance: High compliance rates indicate strong maintenance planning and execution.
7. Downtime as a Percentage of Operating Time
Definition: This KPI measures how much time equipment is unavailable due to maintenance.
How to Measure:
Importance: Keeping downtime low ensures continuous production and maximized profitability.
How to Implement and Track KPI Effectively
Use a CMMS: A Computerized Maintenance Management System (CMMS) automates data collection and provides real-time reports on maintenance KPI.
Set Realistic Targets: Benchmark against industry standards to define achievable goals.
Train Teams on KPI Utilization: Ensure that maintenance staff understand the importance of these metrics and how they impact overall performance.
Regular Performance Reviews: Analyze KPI trends to identify inefficiencies and opportunities for improvement.
Leverage Predictive Analytics: AI-powered tools can enhance KPI tracking by forecasting maintenance needs based on historical data.
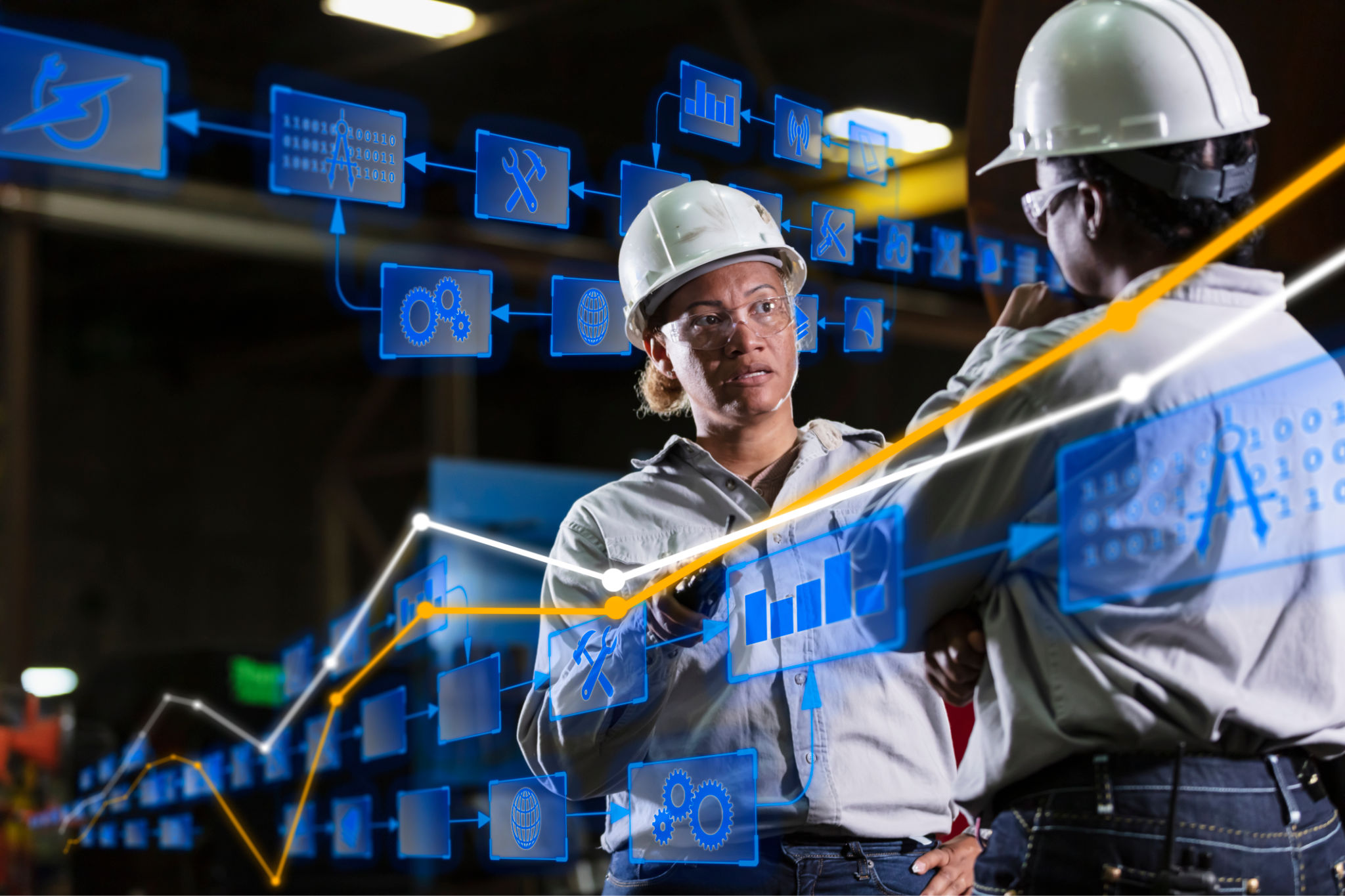
Conclusion: Measuring for Success
Effective maintenance management is driven by data. By monitoring key performance indicators such as MTBF, MTTR, OEE, and work order compliance, organizations can optimize their maintenance strategies, reduce costs, and improve asset longevity.
Call to Action
At RPC Maint, we specialize in helping businesses implement and refine maintenance KPI to drive operational success. Whether you need assistance with CMMS integration, KPI tracking, or maintenance coaching, our expert team is ready to support your journey toward efficiency and cost savings. Contact us today to optimize your maintenance strategy and stay ahead of the competition.
#KPIs #PerformanceMeasurement #MaintenanceSuccess