Shifting Gears: From Reactive to Preventive and Predictive Maintenance
Understanding Maintenance Approaches
In the world of industrial operations, the maintenance department ensures the smooth functioning of machinery and equipment. Even today approximately 60% of businesses rely on reactive maintenance, a strategy that addresses problems as they occur. However, this 'fire-fighting' approach leads to unexpected downtime, increased costs, and a stressed maintenance department. As technology evolves, companies are increasingly shifting towards preventive and predictive maintenance strategies to enhance efficiency, improve equipment availability and safety, and reduce unexpected failures.
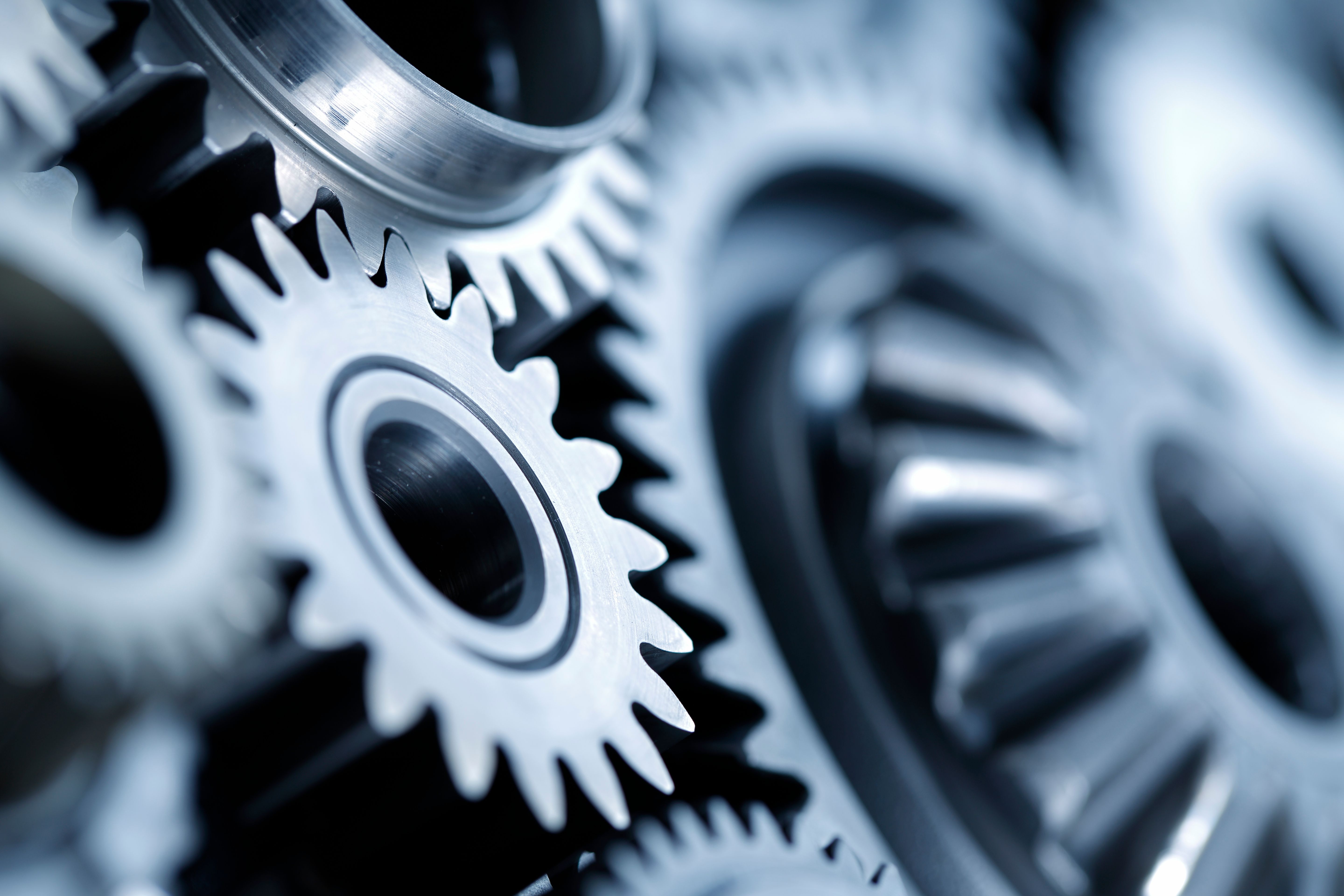
Reactive Maintenance: A Quick Fix Approach
Reactive maintenance, also known as breakdown or corrective maintenance, is the most traditional form of maintenance. It focuses on repairing equipment after it has failed. While this approach might seem cost-effective initially, it often results in higher long-term expenses due to unplanned downtime and potential damage to machinery. Moreover, it can disrupt production schedules and affect overall productivity.
The following shows the advantages and disadvantages of using a reactive maintenance strategy:
Advantages:
- Initially lower maintenance costs
- Less planning
- Simplicity
Disadvantages:
- Higher long-term costs
- Unpredictable downtime
- Shorter equipment lifespan
- Potentially greater safety risks
- Poor asset utilization
- Takes longer, drains resources, and interferes with preventive work
Benefits of Preventive Maintenance
Preventive maintenance is a more proactive approach that involves regular inspections and servicing of equipment to prevent unexpected breakdowns. This strategy is based on predetermined schedules (often calendar based) and manufacturer recommendations. By executing routine checks and maintenance, businesses can significantly extend the lifespan of their equipment.
The key benefits of preventive maintenance include:
- Reduced Downtime: Regular maintenance helps in identifying potential issues before they lead to unexpected failures.
- Cost Savings: By preventing major breakdowns, companies can save on repair costs and avoid revenue loss from a production outage.
- Improved Safety: Regular inspections can identify safety hazards, reducing the risk of accidents in the workplace.
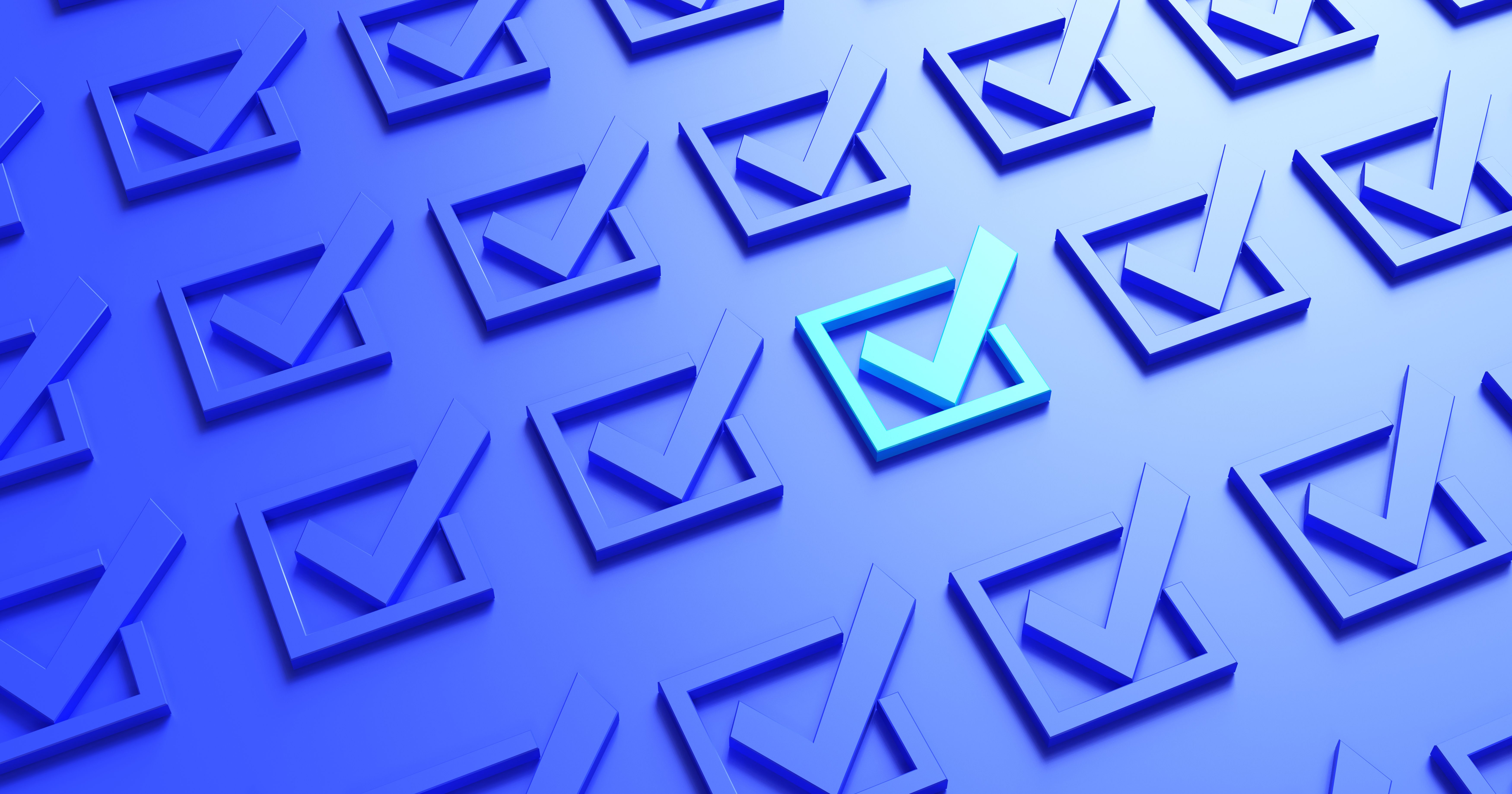
The Role of Predictive Maintenance
Predictive maintenance takes things a step further by using data analysis tools and techniques to predict when equipment failure might occur. This approach relies on condition-monitoring equipment to assess the performance of machinery in real-time. By doing so, it allows for maintenance activities to be scheduled just before a failure is likely to happen, thereby maximizing equipment uptime and reliability.
How Predictive Maintenance Works
Predictive maintenance utilizes technologies such as IoT sensors, machine learning, and AI to monitor equipment conditions continuously. These technologies collect vital data such as temperature, vibration, and lubrication levels. The data is then analyzed to identify patterns that could indicate potential failures. The process involves:
- Data Collection: Using sensors and monitoring tools to gather real-time data from equipment.
- Data Analysis: Applying analytics to interpret the data and predict potential issues.
- Actionable Insights: Providing maintenance teams with insights to schedule repairs before failures occur.
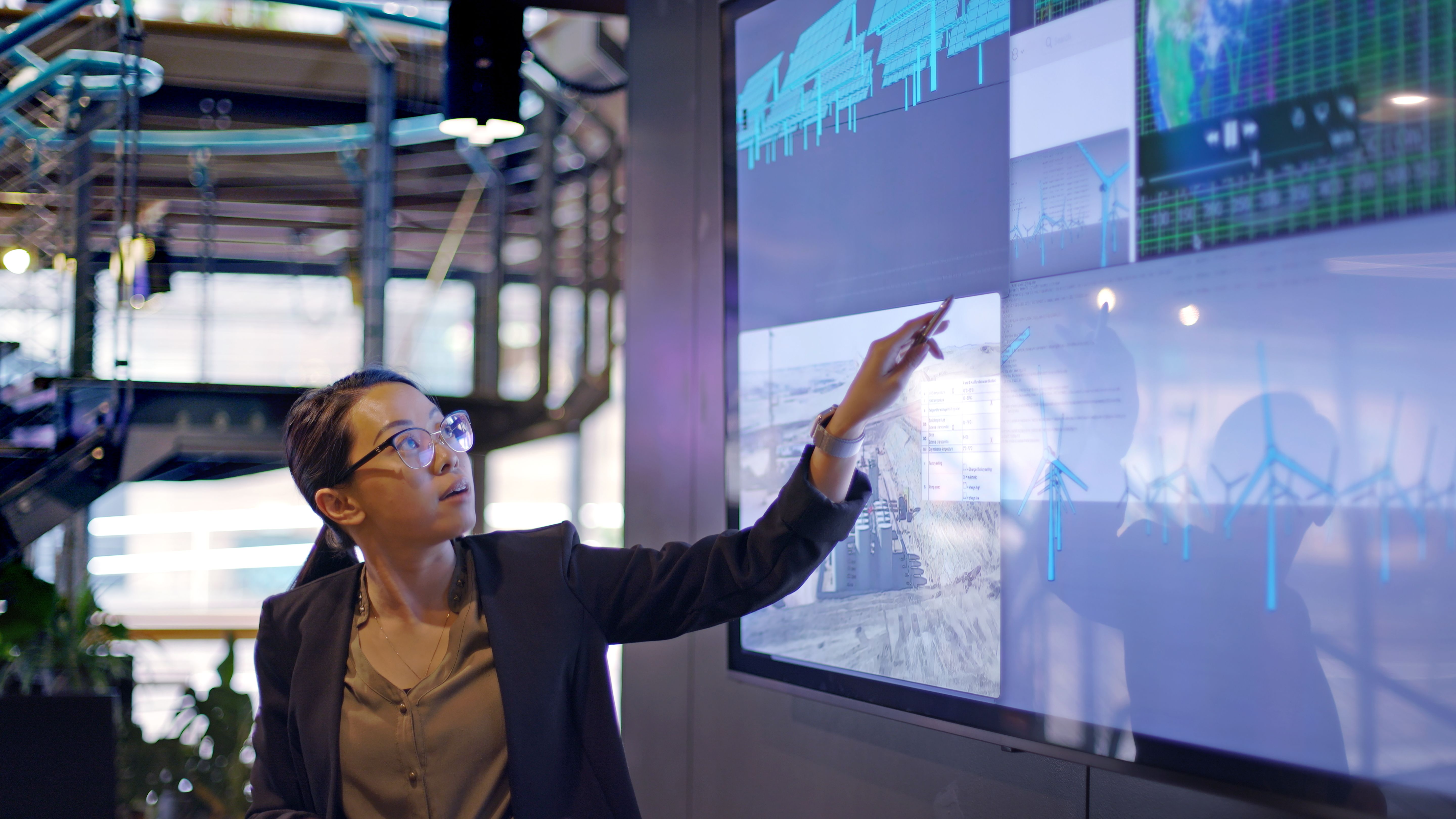
The Future of Maintenance Strategies
The shift from reactive to preventive and predictive maintenance is not merely a trend; it's a necessary evolution in the manufacturing and industrial sectors. As technology and AI continue to advance, these maintenance strategies will become more sophisticated, offering even greater efficiencies and cost savings. Companies that embrace these approaches will likely see improved operational performance and a stronger competitive edge in their industries.
In conclusion, transitioning from reactive to preventive and predictive maintenance can transform how businesses manage their assets. By investing in these modern approaches, companies not only safeguard their equipment but also enhance their operational resilience and profitability. Embracing this shift is essential for any organization aiming for long-term success in an increasingly complex industrial landscape.