6. Beyond the Finish Line: Ensuring Quality in Every Turnaround Phase
In the high-stakes world of Turnaround (TAR) projects, achieving deadlines and budgets is important, but ensuring quality in every phase is non-negotiable. Quality control is the cornerstone of a successful TAR, ensuring that assets meet operational requirements and compliance standards while safeguarding long-term performance. A turnaround without a rigorous focus on quality risks equipment failures, operational inefficiencies, and safety hazards that could have been prevented.
This article explores the key strategies for maintaining quality throughout the TAR lifecycle and highlights why quality should be a priority for every organisation, regardless of the industry or location.
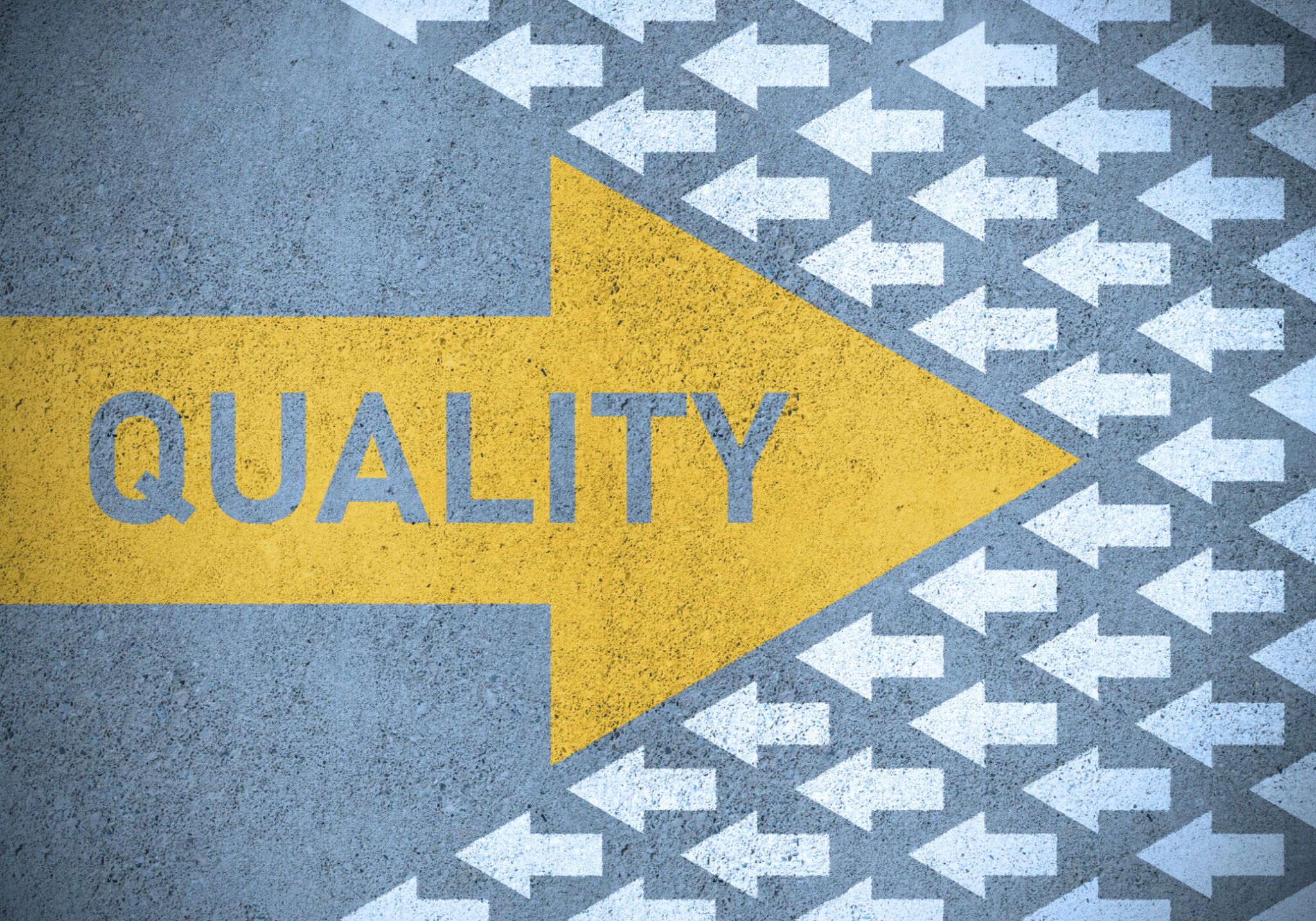
The True Cost of Poor Quality
Failure to prioritize quality can have devastating consequences. Industry research shows that 40% of post-TAR failures stem from inadequate quality assurance during execution and inspection phases. Such failures can lead to costly rework, extended downtime, and even safety incidents. For example, equipment failures in the oil and gas sector can result in $500,000 to $1 million per day in production losses (Johnson, 2022).
Ensuring quality isn’t just about avoiding losses—it’s about maximizing the value of the turnaround. A 2023 study revealed that TARs with robust quality control frameworks achieve 15% higher operational reliability and 20% lower maintenance costs in the years following the project (Smith, 2023).
Best Practices for Quality in TARs
1. Early Quality Integration:
Quality must be built into the TAR from the planning phase. This includes defining Key Performance Indicators (KPIs), such as defect-free start-up rates and compliance with technical standards. Projects with clear quality KPIs report 30% fewer post-TAR failures compared to those without.
2. Third-Party Inspections:
Engaging third-party inspectors during critical phases ensures unbiased assessments of equipment and work quality. According to best practices, 30-40% of TAR quality issues can be identified and rectified before project completion when third-party inspections are conducted (Jones, 2022).
3. Material and Equipment Validation:
Quality checks on incoming materials and equipment are critical. All components must meet the required specifications, and any deviations should be flagged immediately. Projects that implement Material Verification Procedures (MVPs) during procurement reduce rework rates by 25%.
4. Digital Quality Tracking:
Use digital tools like Quality Management Systems (QMS) to track progress, flag deviations, and generate reports in real time. These systems provide visibility into every stage of the TAR and help teams ensure compliance with quality standards. Teams using QMS tools report 20% faster issue resolution (Johnson, 2022).
5. Comprehensive Testing and Commissioning:
The testing and commissioning phase is where the quality of the TAR truly comes to light. Conduct comprehensive checks on all systems, including pressure tests, operational simulations, and performance validations. Have a rigorous pre-start-up safety review (PSSR) in place prior to restarting the facility. Go through each equipment item with the Area Engineers, HSE, and Operations personnel to ensure that the asset is complete and ready for start-up.
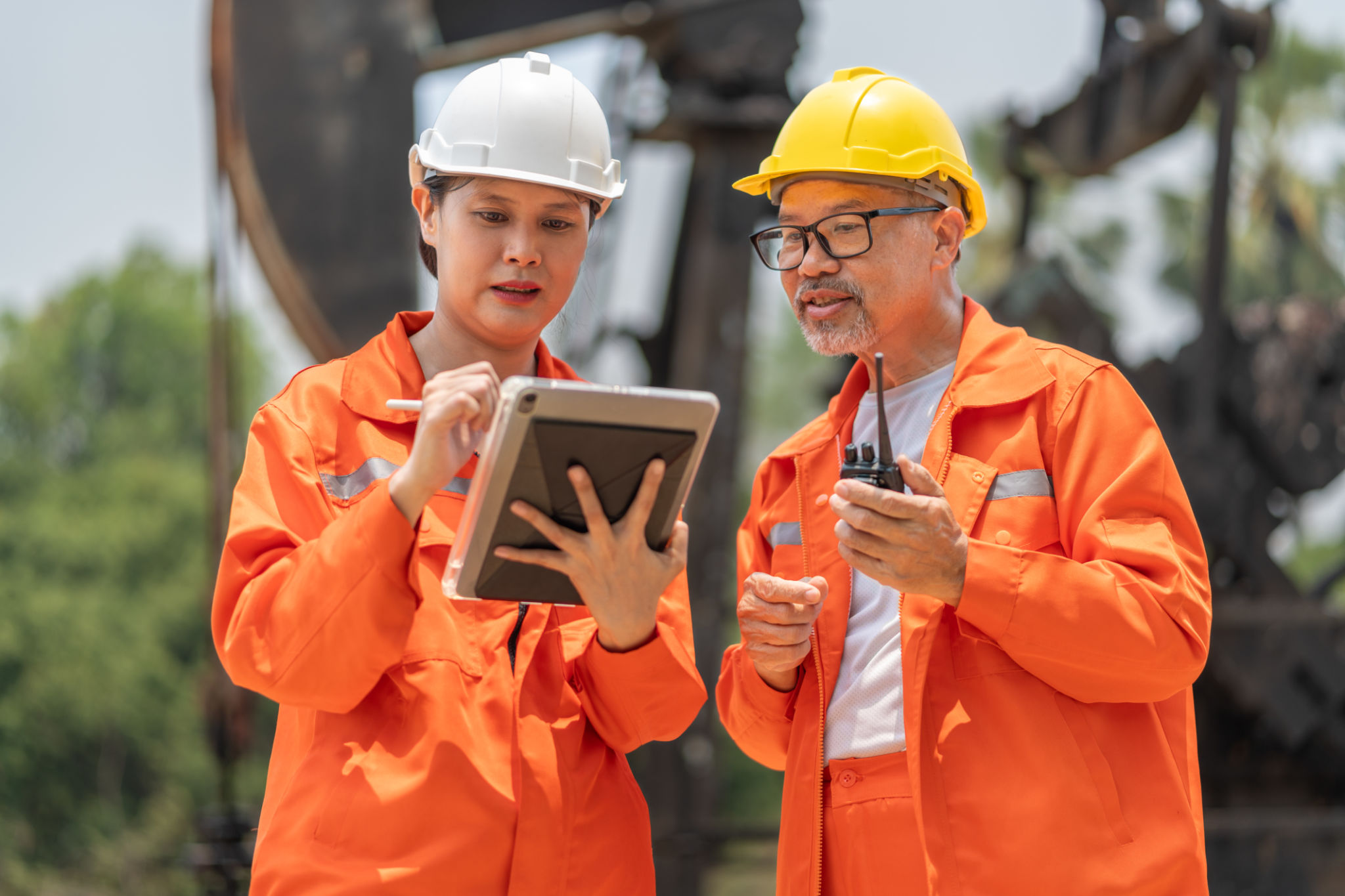
Safety and Quality: A Symbiotic Relationship
Safety and quality are inextricably linked. A poorly executed TAR not only compromises operational efficiency but also endangers lives. For example, a failed pressure vessel inspection can lead to catastrophic outcomes during operation. Ensuring quality in all TAR phases—from planning to execution—significantly reduces safety risks.
- Permit to Work (PTW) systems: Ensure that all work adheres to safety protocols, with detailed quality checks before and after high-risk tasks.
- Toolbox Talks (TBT): Use TBT to highlight the importance of quality in reducing safety hazards.
- Post-TAR Reviews: Conduct detailed reviews to assess the performance of each phase of the TAR, and identify lessons learned for future TARs. All lessons learned should be managed through the Change Management System to ensure they are captured and actioned.
According to OSHA, TAR projects that emphasize quality in parallel with safety experience 50% fewer incidents and achieve smoother start-ups (OSHA, 2021).
Universal Principles for Quality Assurance
The principles of quality assurance apply universally across industries and geographies. Whether executing a TAR in North America, Europe, or Asia, organizations must prioritize quality to ensure long-term success. From oil refineries to chemical plants, the steps outlined above can be adapted to suit specific operational and regulatory requirements.
Call to Action
Quality is not an afterthought—it’s the foundation of every successful TAR. If you’re planning a turnaround, ask yourself: are your quality controls robust enough to ensure a defect-free start-up? Do you have the tools and processes in place to prevent post-TAR failures?
Let’s connect on LinkedIn to discuss how you can integrate industry-leading quality practices into your TAR projects. Together, we can ensure that every phase of your turnaround meets the highest standards of excellence.
Quotes and figures used in this article are taken from RPC Maint (Owned by Paul Coey) Training Materials (2024).
References
Johnson, R. (2022). "Leveraging Digital Tools for Quality Assurance in TARs." Industrial Maintenance Quarterly, 17(2), pp. 30-35.
Jones, S. (2022). "The Role of Third-Party Inspections in Improving TAR Outcomes." Journal of Maintenance and Reliability, 15(4), pp. 45-50.
OSHA. (2021). "Safety and Quality Integration in Industrial Turnarounds." OSHA Reports.
Smith, L. (2023). "Post-TAR Reliability: The Impact of Quality Control." Journal of Project Management, 18(3), pp. 40-45.