5. The Power of Precision: Logistics in Turnaround Success
“The line between disorder and order lies in logistics.” Sun Tzu
“Amateurs talk strategy. Professionals talk logistics.” Omar N. Bradley
When it comes to Turnaround (TAR) projects, logistics is the backbone that supports the entire operation. Without precise and efficient logistics management, even the best-planned TARs can fail due to delays, equipment shortages, and disorganized workflows. The logistics involved in a TAR—whether it’s moving critical equipment, managing contractor schedules, or ensuring materials arrive on time—can determine whether a project finishes on budget and on schedule.
In this article, I will explore the importance of logistics in TARs, highlight best practices, and provide insight into how safety plays a pivotal role in logistics management. Whether you're conducting a TAR in a refinery, chemical plant, or manufacturing facility, precision in logistics is essential for success.
The Cost of Inefficient Logistics
Logistics can be the difference between a smooth project and one plagued by costly delays. Industry data shows that logistics-related delays account for up to 35% of total TAR overruns. With the average TAR costing between $20 million and $50 million, even a small logistics misstep can result in a 10-20% increase in project costs (Smith, 2023). Additionally, any delay in procuring essential materials or equipment directly impacts production, further increasing costs due to extended downtime.
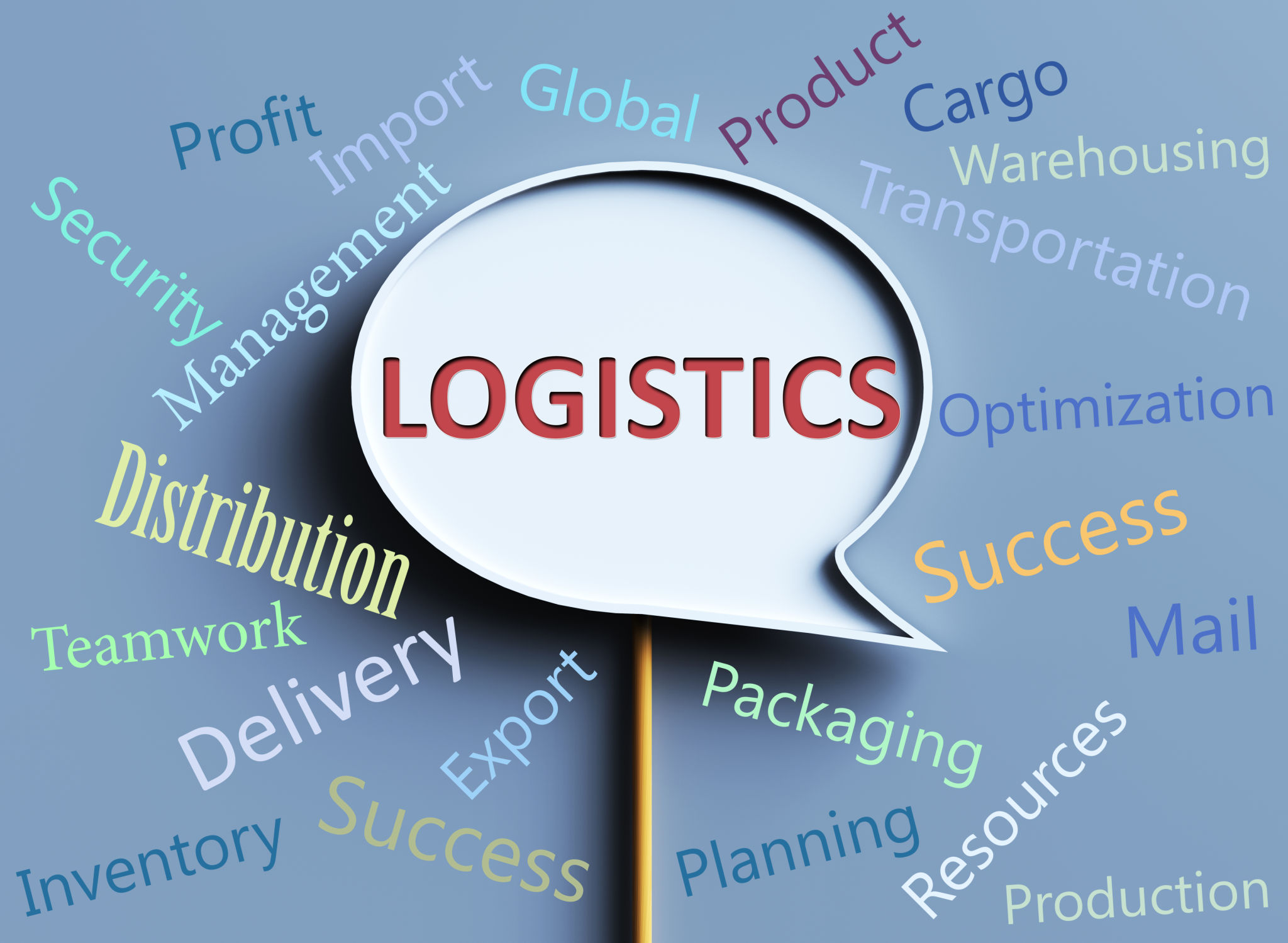
Best Practices in TAR Logistics
1. Detailed Planning and Coordination:
Effective TAR logistics begin long before the execution phase. A comprehensive Logistics Plan should be developed early, mapping out the movement of materials, equipment, and personnel. This plan must also account for potential bottlenecks and address contingencies. Using Project Management Software like Primavera P6 can help track every aspect of logistics in real-time, allowing teams to adjust schedules and reroute materials as needed (Jones, 2022).
2. Just-in-Time (JIT) Delivery:
Adopting JIT principles can significantly reduce storage costs and minimize the risk of damage or theft of materials. However, JIT requires close collaboration with suppliers to ensure that materials arrive precisely when they are needed. According to best practices, 90% of materials should arrive on-site within 48 hours of their planned usage. Failure to achieve this can result in on-site congestion or, worse, equipment downtime waiting for parts.
3. Clear Communication Channels:
One of the biggest challenges in logistics is managing communication between the various stakeholders. Daily Logistics Briefings should be held with contractors, engineers, and the TAR Manager to ensure everyone is aligned on the delivery schedules and any emerging issues. According to a recent study, projects that establish clear logistics communication protocols are 25% more likely to finish on time (Smith, 2023).
4. Technology and Tracking:
Implementing RFID (Radio-Frequency Identification) or GPS Tracking for materials and equipment is now considered best practice in TAR logistics. This technology allows real-time visibility into where equipment is and when it will arrive, helping project managers adjust timelines based on actual delivery data. It’s estimated that companies using RFID tracking reduce logistics delays by up to 30% (Johnson, 2022).
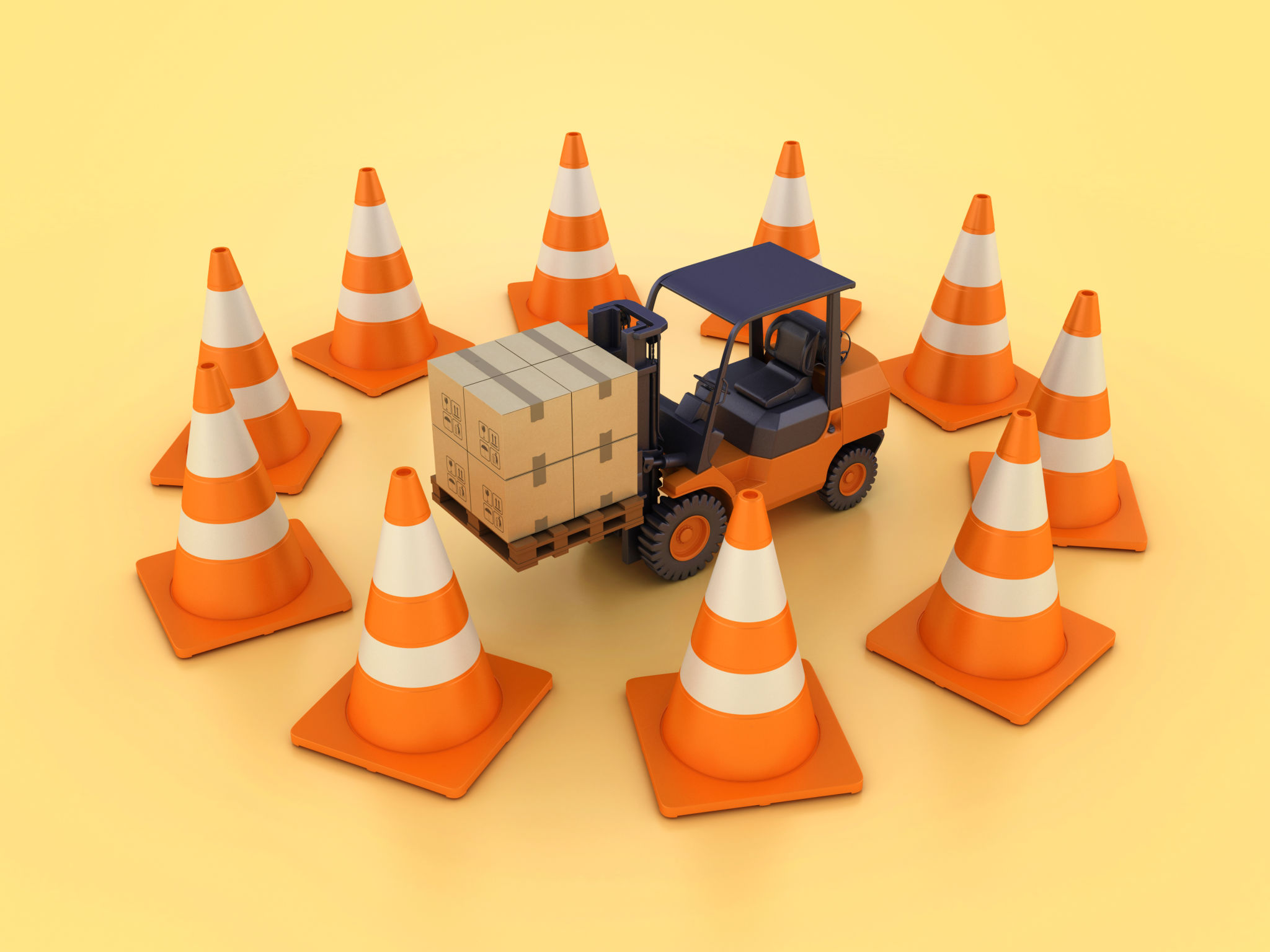
Safety in TAR Logistics
Safety must be integral to all logistics operations during a TAR. The movement of heavy machinery, tools, and materials presents numerous hazards, which is why safety protocols must be established from the start.
5. Safe Material Handling:
Equipment such as cranes and forklifts must be regularly inspected and certified for use. Contractors handling heavy loads must be properly trained and equipped with the necessary Personal Protective Equipment (PPE), including gloves, helmets, and visibility vests. According to OSHA, 50% of TAR accidents involving logistics occur due to improper material handling and lack of PPE (OSHA, 2021).
6. Traffic Management Plans:
On-site traffic can be a major safety hazard if not properly controlled. A Traffic Management Plan (TMP) should be developed, specifying vehicle routes, loading and unloading zones, lay-down areas, and pedestrian walkways. Sites with a TMP see 20% fewer accidents related to vehicle and equipment movement (Jones, 2022).
7. Emergency Preparedness:
Every TAR logistics plan must include emergency response protocols for incidents such as equipment failure, fire, or personnel injury. Ensuring that materials and equipment are stored safely, with appropriate fire hazards and access routes, reduces the risk of catastrophic incidents.
Applying These Principles Globally
The need for precision in logistics applies regardless of where you’re conducting a TAR. Wherever you are, the principles of efficient material handling, JIT delivery, and communication protocols are universal. The focus should always be on optimizing logistics to minimize costs, improve efficiency, and ensure safety on-site.
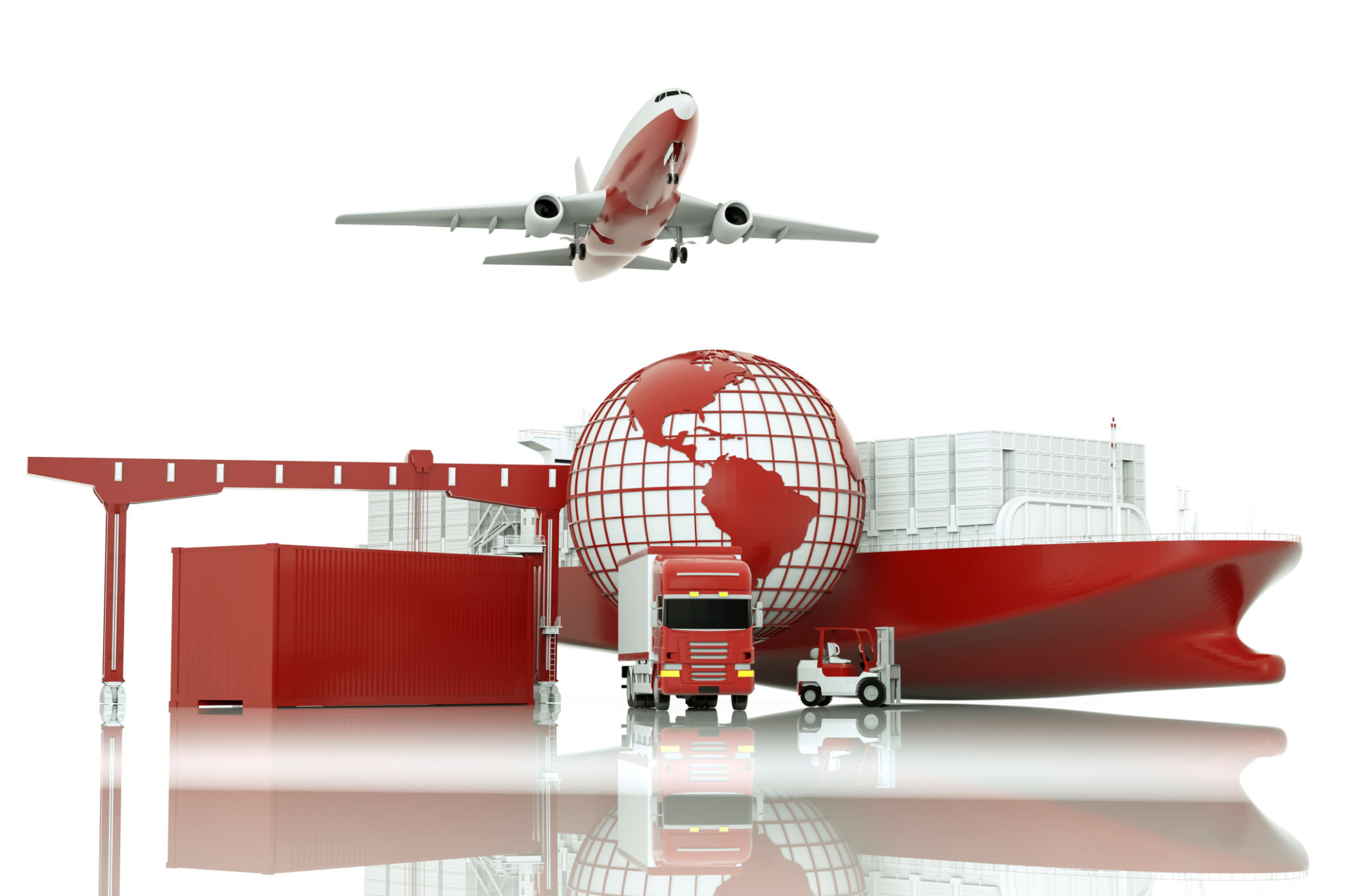
Call to Action
Logistics are the lifeblood of a successful TAR. If you want to enhance the efficiency of your next turnaround or discuss how to implement best practices for logistics, connect with me on LinkedIn. Together, we can ensure that your project runs smoothly, safely, and on time.
References:
Coey, P. (2024). RPC Maint Training Materials.
Johnson, R. (2022). "The Role of RFID and GPS Tracking in Industrial Logistics." Logistics and Supply Chain Management Review, 12(3), pp. 30-35.
Jones, S. (2022). "Managing On-Site Traffic During Turnarounds." Project Execution Quarterly, 24(2), pp. 18-22.
OSHA. (2021). "Preventing Material Handling Accidents During TARs." OSHA Safety Reports.
Smith, L. (2023). "Best Practices for Just-in-Time Delivery in Industrial Projects." Journal of Project Management, 25(1), pp. 50-58.