1. Laying the Groundwork: Setting the Stage for a Successful Turnaround
In the world of industrial maintenance, Turnaround (TAR) projects are some of the most complex and resource-intensive events an organization will face. They require careful planning, immense coordination, and unwavering attention to safety and efficiency. The importance of the initiation phase cannot be overstated. It sets the foundation for everything that follows. Whether you're preparing for a turnaround at a refinery, petrochemical plant, or a paper mill, the principles for laying the groundwork remain the same.
Understanding the Cost and Complexity of TARs
A TAR involves the shutdown of an entire process unit for maintenance, inspection, and refurbishment. According to industry benchmarks, the cost of a TAR can range between $20 million and $50 million, depending on its scale. For a facility with a capacity of 250,000 barrels per day, losing just one day of production at $50 per barrel means $12.5 million in lost revenue every single day the plant is offline.
This stark financial reality is compounded by the complexity of TARs, which involve thousands of tasks performed by a small army of contractors, engineers, and operational staff. Failing to properly initiate and plan a TAR can lead to delays, cost overruns, and, in the worst cases, safety incidents. To minimize these risks, we must apply global best practices, ensuring that safety, planning, and stakeholder engagement are built into every step of the process.
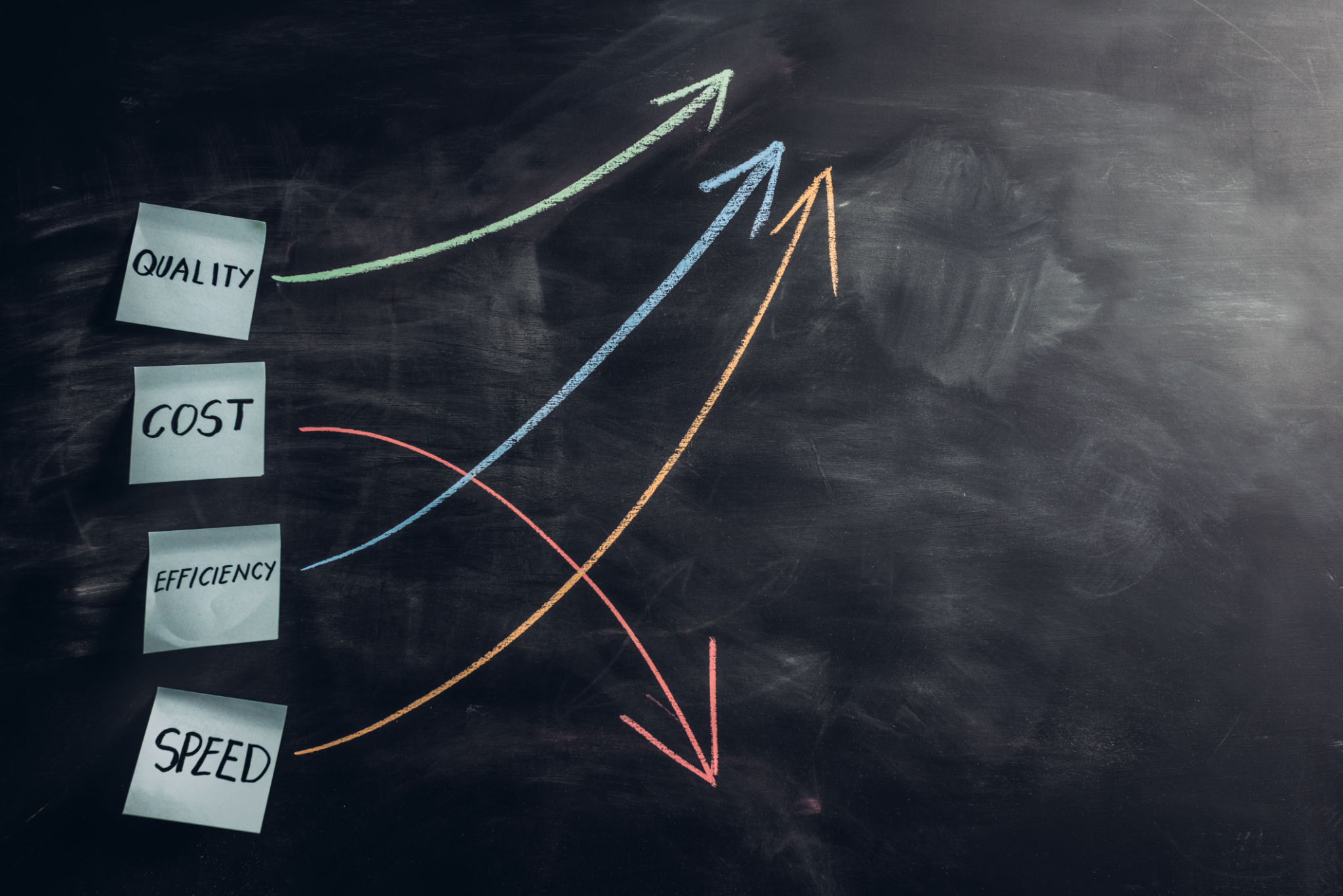
Best Practices for a Robust Initiation Phase
1. Stakeholder Engagement:
Identifying and involving all key stakeholders at the outset is critical. This should include senior management, engineers, operations staff, contractors, and the Steering Committee. Early engagement helps define expectations, roles, and responsibilities, which reduces the risk of miscommunication later in the project.
2. Risk and Safety Assessment:
The initiation phase must also involve a comprehensive risk and safety assessment. A recent study found that up to 40% of all TAR accidents occur due to a lack of proper planning and risk identification. Ensure that a Risk Assessment Matrix (RAM) is developed early, covering all potential hazards, and that safety is prioritized throughout the turnaround.
3. Communication Channels:
Establishing clear communication pathways from the outset is another essential best practice. According to the Project Management Institute (PMI), TAR projects that establish robust communication channels between stakeholders have a 30% higher success rate than those that do not. This means regular briefings, updates, and a solid Single Point of Responsibility (SPR) for each task.
4. Scope Definition:
The initiation phase is where the scope of the TAR is determined. The Scope of Work (SoW) should be meticulously detailed to avoid the risk of scope creep, which can lead to cost increases and schedule overruns. Industry data suggests that projects with poorly defined scopes experience up to 20% budget overruns.
Emphasizing Safety from Day One
Safety is non-negotiable in TAR projects. The Permit to Work (PTW) system, the use of Personal Protective Equipment (PPE), and the Lock-Out Tag-Out (LOTO) procedures must all be established before the project begins. In a study conducted by the Occupational Safety and Health Administration (OSHA), 60% of TAR-related injuries were preventable through more rigorous planning and safety protocols. As a leader or stakeholder in the TAR process, it’s your responsibility to ensure that the safety measures put in place are followed diligently, from initiation to closeout.

Applying Best Practices Across Industries
Whether you’re conducting a TAR in the petrochemical sector or the power generation industry, these principles remain universally applicable. The TAR Clock (see RPC Maint’s training course) serves as a useful guide for tracking the stages of a turnaround, ensuring that nothing is left to chance. A well-executed initiation phase will not only reduce risk but also improve efficiency, resulting in faster turnaround times and fewer incidents.
Remember, the success of a TAR is not only measured by how quickly the plant is back online but by how safely and cost-effectively this is achieved.
Call to Action
As you plan your next TAR, take the time to evaluate your initiation phase. Are all stakeholders engaged? Have you defined your scope and assessed your risks? Is safety prioritized at every step? By focusing on these areas early, you’ll set your project up for success.
To discuss how these principles can be applied to your specific TAR project or to explore new strategies for managing complex shutdowns, connect with me on LinkedIn. Let’s ensure that every turnaround you manage is a success, from initiation to closeout.